Increased response speed
The MR-J3's 900Hz speed-frequency response rate is over 30% faster than exist- ing models. For users this means faster operation, greater precision, faster retool- ing in production, less wastage and better product quality.
Designed for challenging tasks
Every detail of the MR-J3 series is designed for performance and reliability, from the intelligent drive electronics to the robust mechanical components. These next-gen- eration servo systems are both compact and flexible, featuring Plug & Play function- ality, fibre-optics technology and optical feedback systems.
Reduced component size
The reduced component size is critically important to machine designers who are often called upon to sqeeze all of the con- trol solutions they need into the smallest deliverable package. The MR-J3 series boasts an intelligent design that has reduced amplifier sizes by up to 40 % and motor lengths by almost a quarter. This means machine designers don't have to make as many compromises to get the right motor and deliver the right power in the right place. These servos' compact dimensions enable flexible installation and economical design, which helps you to keep your costs down and be more com- petitive in the global economy.
Firmware that delivers performance
All MR-J3 servo amplifiers use the very lat- est regulation and control technologies. These systems ensure fast installation and setup and make it possible to configure sta- ble systems with very short response times – no matter what your application.

Real-time auto-tuning
The real-time auto-tuning function sets the servo's control parameters automatically, eliminating the need to calibrate the sys- tem for each individual application. But that's not all – auto-tuning also works con- tinuously while the system is in operation, making constant adjustments to cater for applications with fluctuating moments of inertia. This makes it possible to use these servos in a much wider range of applica- tions.
Adaptive filtering
Adaptive filters ensure dynamic response and vibration-free operation, even in more demanding applications with suspended loads and high friction coefficients.
Advanced suppression of mechanical vibration
The MR-J3 has an automatic feature that enables the amplifier to minimize the effects of a vibrating load. In another first, this innovative function can also suppress vibrations at the end of a tool arm as well as those in the drive train.
Software that makes your life easier
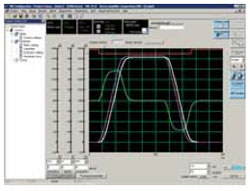 The MR Configurator software package makes configuration and diagnostics quick and easy and includes powerful graphical machine analysis and simulation functions. Machine analysis enables determination of the frequency response of the connected drive train without any additional instru- ments. If necessary, you can then make design changes or install filters to achieve better machine performance. The system can be connected to a personal computer with a standard USB (Universal Serial Bus) port.
A wide range of automatic configuration assistants make it easy to set up your new servo systems correctly, even for less expe- rienced users.
Advanced features
Increased motor speed
MR-J3 motors lead the market, combining speeds of up to 6,000rpm with high torques. This makes it easier for designers to select the motors they need to meet tough performance criteria.
Increased encoder resolution
All MR-J3 encoders are 18 bit, delivering an industry-leading 262,144 pulses per revolu- tion. This high resolution makes it possible to detect and suppress mechanical vibra- tions. The non-volatile absolute encoder system has a backup battery, eliminating the need for time-wasting zero-point calibration routines.
Improved motor IP ratings
All MR-J3 motors are IP65 rated as standard (all 400 V motors are IP67). This means that MR-J3 systems can be used in heavy-duty industrial environments.
Specifications
MR-J3-A/B
Performance |
10A 10B 0.1kW |
20A 20B 0.2kW |
40A 40B 0.4kW |
70A 70B 0.7kW |
60A(4) 60B(4) 0.6kW |
100A(4) 100B(4) 1kW |
200A(4) 200B(4) 2kW |
350A(4) 350B(4) 3.5kW |
500A(4) 500B(4) 5kW |
700A(4) 700B(4) 7kW |
Power supply |
3~ 200 – 230 V AC, 50/60 Hz; 1~ 200 – 230 V AC, 50/60 Hz |
3~ 200 – 230 V AC, 50/60 Hz (200 V type without (4)); 3~ 380 – 480 V AC, 50/60 Hz (400 V type with (4)) |
Control system |
Sinusoidal PWM control / current control system / analog, digital, SSCNET III |
Dynamic brake |
Built-in |
Protective functions |
Overcurrent shutdown, regeneration overvoltage shutdown, overload shutdown (electronic thermal), servomotor overheat protection, encoder fault protection, regeneration fault protection, undervoltage / sudden power outage protection, excess error protection |
Structure/protection |
Self-cooling, open (IP00); from 70A/B (200 V) and 200A4/B4 (400 V) fan-cooling, open (IP00) |
Environment |
Ambient temperature |
Operation: 0 – 55 °C (no freezing); Storage: -20 – 65 °C (no freezing) |
Ambient humidity |
Operation: 90 % RH max. (no condensation); Storage: 90 % RH max. (no condensation) |
Others |
Elevation: 1000 m or less above sea level; Oscillation: 5.9 m/s (0.6 G) max. |
|